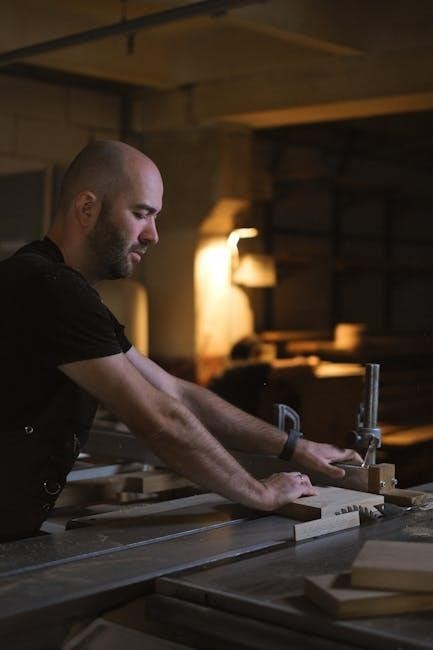
Table saw guide rollers are essential components that ensure smooth, precise, and safe cutting operations. They help maintain material stability, reduce friction, and prevent kickback, enhancing overall woodworking efficiency and accuracy.
1.1 What Are Guide Rollers and Their Purpose
Guide rollers are cylindrical components attached to a table saw’s fence system, designed to smoothly guide materials during cutting; They reduce friction, preventing wood from binding or kicking back. Made from durable materials like steel or ceramic, these rollers ensure consistent control and accuracy. Their primary purpose is to enhance safety and precision, making them indispensable for both professional and hobbyist woodworking projects.
1.2 Importance of Guide Rollers in Table Saw Operations
Guide rollers play a crucial role in ensuring precise, safe, and efficient table saw operations. They provide smooth material control, reducing friction and vibration, and help prevent dangerous kickbacks. By maintaining consistent alignment and support, guide rollers enhance cutting accuracy and stability. Their presence minimizes the risk of uneven cuts and improves overall workflow, making them an indispensable feature for both amateur and professional woodworking projects.
Types of Guide Rollers Available
Guide rollers come in various types, including sealed bearing, ceramic, and steel options, each offering distinct advantages in terms of durability, load capacity, and precision for woodworking tasks.
2.1 Sealed Bearing Guide Rollers
Sealed bearing guide rollers are designed for durability and smooth operation. They feature enclosed bearings that protect against dust and debris, ensuring consistent performance. These rollers are ideal for heavy-duty applications, as they minimize friction and maintain accuracy. Their sealed construction reduces the need for frequent lubrication, making them a low-maintenance choice for woodworking professionals and hobbyists alike. They are particularly suited for demanding table saw environments where reliability is crucial.
2.2 Ceramic vs. Steel Guide Rollers
Ceramic guide rollers offer exceptional hardness and wear resistance, making them ideal for precise cuts and long-term durability. Steel rollers, while tougher, excel in heavy-duty applications due to their superior impact resistance. Ceramic rollers reduce friction for smoother operation, while steel rollers are preferred for industrial settings where strength is critical. Choosing between them depends on workload demands and the need for either precision or rugged reliability.
Installation and Setup of Guide Rollers
Proper installation and alignment of guide rollers are crucial for optimal table saw performance. Ensure rollers are securely fastened, aligned, and tensioned correctly for smooth, accurate cuts and enhanced safety.
3.1 Step-by-Step Installation Guide
Installing guide rollers involves aligning and securing them to the table saw’s frame. Begin by disconnecting power, then attach the rollers to the designated mounts. Adjust the roller positions to ensure proper material guidance. Tighten all bolts firmly and test the system for smooth operation. Proper installation ensures accuracy, reduces vibration, and prevents kickback, enhancing overall safety and efficiency in woodworking projects.
3.2 Aligning Guide Rollers for Optimal Performance
Proper alignment of guide rollers is critical for precise cutting and safety. Use an Allen wrench to adjust the rollers, ensuring they are parallel to the table saw’s surface. Align the rollers with the blade, maintaining even spacing to prevent material binding. Test the setup by feeding a straightedge or scrap wood through the saw. Proper alignment ensures smooth material feeding, reduces vibration, and minimizes the risk of kickback, optimizing overall performance and safety.
Maintenance and Care of Guide Rollers
Regularly clean guide rollers to remove debris and apply lubricant to bearings for smooth operation. Inspect for wear and damage, replacing parts as needed to ensure optimal performance and safety.
4.1 Cleaning and Lubricating Guide Rollers
Regular cleaning and lubrication of guide rollers are crucial for maintaining smooth operation. Use compressed air or a soft brush to remove dust and debris. Apply a high-quality, non-stick lubricant to moving parts to reduce friction and wear. Avoid using heavy oils that attract dust. Clean and lubricate after every project or when visible buildup occurs. Proper maintenance ensures consistent performance and extends the lifespan of your guide rollers.
4.2 When to Replace Worn-Out Guide Rollers
Replace guide rollers when they show excessive wear, such as uneven surfaces, rust, or play. If rollers no longer glide smoothly or cause misalignment, it’s time for new ones. Worn rollers can lead to inaccurate cuts and safety hazards. Inspect them regularly for damage or corrosion. Replace promptly to maintain precision and reliability in your table saw operations. Deteriorated rollers compromise both performance and safety, so don’t delay replacement.
Choosing the Right Guide Rollers for Your Table Saw
Selecting guide rollers involves considering factors like durability, load capacity, and material type. Opt for high-quality options from reputable brands to ensure reliability and performance for precise cuts.
5.1 Factors to Consider (Durability, Load Capacity, etc.)
When selecting guide rollers, prioritize durability and load capacity to handle heavy materials. Consider the roller’s material, such as steel or ceramic, for longevity. Ensure compatibility with your table saw’s design and the types of projects you undertake. Proper alignment and smooth operation are also crucial for accurate cuts and safety. Always choose rollers that meet your specific woodworking needs.
5.2 Top Brands and Models Available in the Market
Leading brands like SawStop, JessEm Tool Company, and Delta offer high-quality guide rollers. SawStop is renowned for its safety-focused designs, while JessEm’s Clear-Cut system excels in reducing kickback. Delta’s rollers are durable and compatible with various table saw models. These brands provide innovative solutions, ensuring precision and reliability for woodworking professionals and enthusiasts alike.
Safety Considerations with Guide Rollers
Proper alignment and regular maintenance of guide rollers are crucial to prevent kickback. Always wear safety goggles and ensure hands are clear of the blade path.
6.1 Preventing Kickback and Other Hazards
Preventing kickback requires proper alignment of guide rollers and ensuring materials are fed smoothly. Keep rollers clean and well-lubricated to avoid jams. Always use a sharp blade and maintain proper fence alignment. Never reach near the blade during operation, and use push sticks for smaller cuts. Regular inspections and timely replacement of worn parts further enhance safety, minimizing risks and ensuring precise cutting.
6.2 Proper Handling and Safety Precautions
Always wear safety goggles, ear protection, and a dust mask when operating a table saw. Ensure loose clothing and long hair are secured. Keep hands away from the blade and use push sticks for smaller cuts. Maintain a firm grip on materials and avoid overreaching. Regularly inspect guide rollers for damage or wear. Proper handling and adherence to safety protocols significantly reduce accidents and ensure a safe woodworking environment.
Advanced Features and Accessories
Modern guide rollers now feature motorized systems, anti-kickback devices, and precision alignment tools, enhancing accuracy and efficiency for professional-grade woodworking projects and intricate cuts.
7.1 Anti-Kickback Devices and Their Integration
Anti-kickback devices are integrated with guide rollers to enhance safety by preventing workpieces from being thrown back during cutting. These devices detect improper stock movement and automatically adjust, reducing the risk of accidents. Their integration ensures smoother operations, improved control, and increased precision, making them a crucial accessory for table saw setups, especially during ripping operations where kickback is most common.
7.2 Upgrading to Motorized Guide Rollers
Upgrading to motorized guide rollers enhances precision and efficiency in table saw operations. These systems automate material feeding, reducing manual effort and minimizing human error. Motorized rollers often feature variable speed controls, allowing for consistent feed rates tailored to specific materials. They integrate seamlessly with anti-kickback devices, ensuring safer and more controlled cuts. This upgrade is ideal for professionals seeking to streamline their workflow and improve overall workshop productivity.
Troubleshooting Common Issues
Common issues with guide rollers include wobbling, misalignment, or excessive noise. Regular maintenance, such as lubrication and alignment checks, can often resolve these problems effectively.
8.1 Diagnosing Wobbling or Misalignment
Diagnosing wobbling or misalignment in guide rollers involves inspecting their installation, checking for wear, and ensuring proper alignment with the table saw fence. Start by verifying that the rollers are securely fastened and free from debris. Use an Allen wrench to tighten any loose mounting hardware. If wobbling persists, inspect the bearings for damage or excessive play. Misalignment can often be corrected by adjusting the roller positions or replacing worn components. Regular lubrication and cleaning can prevent these issues.
8.2 Resolving Noise or Vibration Problems
Noise or vibration issues with guide rollers often stem from loose components, worn bearings, or debris buildup. Start by tightening all mounting hardware and ensuring the rollers are securely fastened. Inspect the bearings for wear and replace them if necessary. Clean the rollers thoroughly to remove dust or debris that may cause friction. Lubricating the bearings can also help reduce noise and vibration, ensuring smoother operation of your table saw.
Expert Tips for Maximizing Guide Roller Efficiency
Expert tips focus on fine-tuning your table saw setup and ensuring guide rollers are properly aligned. Regular lubrication and cleaning enhance performance, enabling precise and smooth cuts consistently.
9.1 Fine-Tuning Your Table Saw Setup
Fine-tuning your table saw setup involves precise alignment of guide rollers with the blade to ensure smooth material flow. Regularly inspect and adjust the rollers for proper tension and alignment. Clean and lubricate moving parts to reduce friction and wear. Test the setup with scrap material to confirm accuracy and consistency. These adjustments enhance cutting precision, safety, and overall productivity, making your woodworking projects more efficient and professional.
9.2 Using Guide Rollers for Precision Cutting
Guide rollers play a crucial role in achieving precise cuts by maintaining material alignment and reducing vibration. They ensure consistent contact between the workpiece and the saw, minimizing kickback risks. Properly adjusted rollers enable smooth, accurate cuts across various materials, from wood to metal. Regular maintenance and alignment are essential for optimal performance, ensuring your table saw delivers professional-grade results consistently.
Comparison with Other Cutting Guides
Guide rollers offer superior versatility compared to laser guides and traditional fences, providing smoother material movement and reduced kickback, making them ideal for precise and safe woodworking operations.
10.1 Guide Rollers vs. Laser Guides
Guide rollers and laser guides serve different purposes in woodworking. Guide rollers provide physical support and reduce kickback, enhancing safety and accuracy. Laser guides offer visual alignment but lack physical material control. While lasers improve visibility, rollers ensure smoother, safer cuts. For precise, hands-on cutting, guide rollers are preferred, especially in preventing accidents and maintaining material stability during operations.
10.2 How Guide Rollers Compare to Traditional Fences
Guide rollers differ from traditional fences in functionality and design. While traditional fences provide rigid support and alignment, guide rollers offer smoother material movement and reduced kickback. Rollers enhance safety and precision, especially for delicate cuts, whereas fences are known for durability and straightforward alignment. Each option caters to specific woodworking needs, with rollers excelling in versatility and fences in robust stability for heavy-duty tasks.
Table saw guide rollers are indispensable for modern woodworking, offering enhanced safety, precision, and efficiency. Investing in high-quality rollers ensures superior performance and longevity for your table saw setup.
11.1 The Role of Guide Rollers in Modern Woodworking
Guide rollers play a pivotal role in modern woodworking by ensuring precise material control, reducing kickback risks, and enhancing cut accuracy. They are integral to maintaining safety and efficiency, making them indispensable for both professionals and hobbyists. Their ability to handle various materials and improve overall table saw performance solidifies their importance in contemporary woodworking practices and setups.
11.2 Encouragement to Invest in High-Quality Guide Rollers
Investing in high-quality guide rollers is a wise decision for any woodworker. They enhance safety by minimizing kickback risks, improve cut precision, and ensure smoother material flow. Durable rollers reduce maintenance needs and extend tool lifespan, making them a valuable long-term investment for professionals and hobbyists alike. Prioritizing quality ensures optimal performance and reliability, elevating your woodworking experience and results.
Leave a Reply
You must be logged in to post a comment.