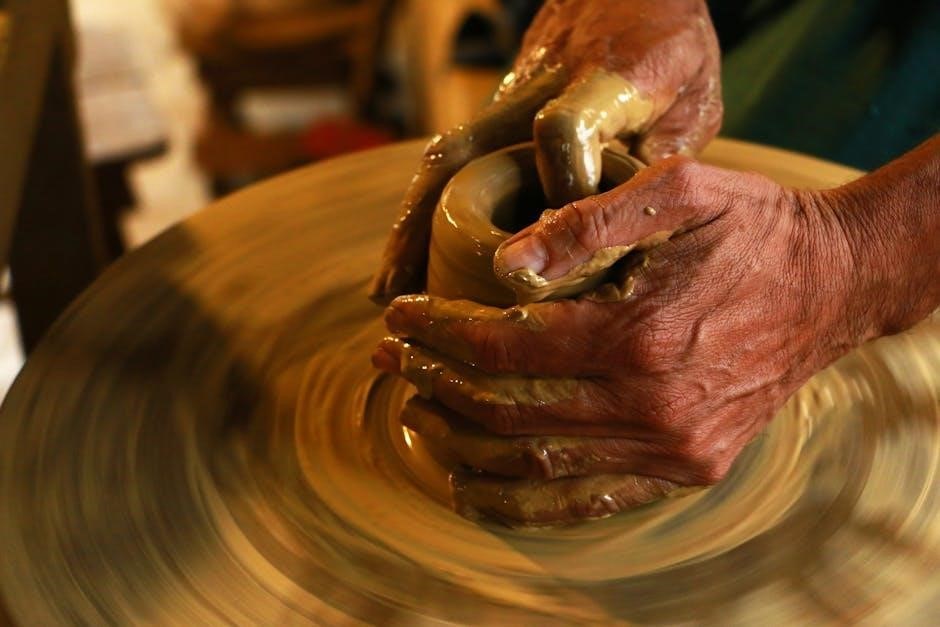
Manual valves are devices controlling fluid flow in systems. They include gate, globe, and ball valves, widely used in plumbing, HVAC, and industrial processes, offering simplicity and reliability.
1.1 Definition and Purpose
A manual valve is a device used to control the flow of liquids, gases, or semi-solids in a system. It operates without automation, relying on physical activation, such as turning a handle or wheel. These valves are essential in plumbing, HVAC, and industrial processes, offering precise control over fluid movement. Their simplicity and reliability make them a crucial component in various systems, ensuring efficient operation and safety.
1.2 Brief History and Evolution
Manual valves have a long history, with early examples dating back to ancient civilizations using primitive valve systems for water control. The industrial revolution brought significant advancements, introducing metallic materials and standardized designs. Over time, manual valves evolved to incorporate various types, such as gate, globe, and ball valves, each tailored for specific applications. Modern materials and engineering have further enhanced their performance, reliability, and safety, making them indispensable in diverse industries today.
Types of Manual Valves
Manual valves include gate, globe, ball, and butterfly valves, each designed for specific applications. They vary in design, operation, and suitability for different fluid control systems.
2.1 Gate Valves
Gate valves are widely used for controlling fluid flow. They feature a movable gate that opens or closes the valve. Designed for on/off operation, they are ideal for systems requiring minimal flow restriction. Gate valves are durable, with sturdy constructions suitable for high-pressure applications. They are commonly found in plumbing, industrial processes, and HVAC systems, offering reliable performance and long service life when properly maintained. Their simplicity makes them a cost-effective choice for many industries.
2.2 Globe Valves
Globe valves are designed for precise flow control, featuring a globe-shaped body with a movable disc. They regulate fluid flow by adjusting the disc’s position, allowing for both on/off and throttling operations. Their design minimizes flow restriction and provides excellent control, making them suitable for applications requiring adjustable flow rates. Commonly used in HVAC and industrial systems, globe valves offer durability and versatility, though they may require more maintenance compared to other valve types due to their complex structure.
2.3 Ball Valves
Ball valves operate by rotating a spherical element with a bored center, controlling fluid flow. They are known for their durability, ease of use, and ability to provide a tight seal. Commonly used in industrial and plumbing systems, ball valves offer reliable performance with minimal maintenance. Their simple design allows for quick operation, making them ideal for applications requiring precise control over fluid or gas flow. They are also resistant to leakage and corrosion, enhancing their longevity.
2.4 Butterfly Valves
Butterfly valves regulate fluid flow using a rotating disk, offering precise control in systems. Their compact design makes them ideal for applications with limited space. Commonly used in water supply, HVAC, and industrial processes, butterfly valves provide efficient operation and easy maintenance. They are known for their quick response and ability to handle high-pressure systems effectively. Their durable construction ensures long-term reliability in various operational environments.
Operation and Working Principles
Manual valves operate through mechanical or actuated controls, regulating fluid flow by opening, closing, or partially obstructing passageways. Their functionality relies on precise engineering and materials.
3.1 Mechanical Operation
Manual valves function through mechanical operation, where a handle or handwheel controls the valve’s movement. Turning the handle rotates the valve stem, which opens or closes the valve. Gate valves, for example, use a threaded stem to lift or lower the gate, while ball valves rotate a ceramic or metal ball to allow or block flow. This simple yet effective mechanism ensures precise control over fluid or gas flow in various systems.
3.2 Hydraulic and Pneumatic Actuation
Hydraulic and pneumatic actuation systems automate manual valve operation, using pressurized fluid or air to control valve movement. These systems are commonly used in industrial settings for precise and rapid valve operation. Hydraulic actuators rely on pressurized fluid, while pneumatic systems use compressed air or gas. Both types often include solenoid valves, control modules, and cylinders to manage flow and pressure, enabling efficient automation in various industrial processes and applications. Regular maintenance is essential for optimal performance.
3.3 Valve Materials and Construction
Manual valves are constructed from durable materials like brass, stainless steel, PVC, and cast iron to ensure longevity and resistance to corrosion. The choice of material depends on the application, with stainless steel ideal for high-pressure systems and PVC suitable for corrosive environments. Valves are typically assembled using precise machining processes, ensuring tight seals and smooth operation. Proper material selection and construction are critical for reliable performance in various industrial and plumbing applications. Regular maintenance extends service life.
Applications of Manual Valves
Manual valves are essential in plumbing, HVAC, and industrial systems, controlling fluid flow. They regulate water, gas, and steam in various settings, ensuring efficient system operation.
4.1 Plumbing Systems
Manual valves are crucial in plumbing systems for controlling water flow. They are used in residential and commercial settings to regulate pressure, prevent backflow, and isolate sections for maintenance. Gate and ball valves are commonly installed in water supply lines, while globe valves are ideal for throttling flow. Regular inspection and maintenance ensure optimal performance and prevent leaks. Proper installation and timely repairs are essential for system reliability and longevity.
4.2 HVAC Systems
Manual valves play a vital role in HVAC systems for temperature regulation and fluid control. Thermostatic radiator valves (TRVs) are commonly used to manage heat distribution in radiators, ensuring efficient energy use. These valves adjust water flow based on ambient temperature, optimizing system performance. Regular maintenance, such as inspecting for leaks and cleaning, is essential to ensure proper functionality. Proper valve operation helps maintain consistent indoor temperatures and reduces energy costs.
4.3 Industrial Processes
Manual valves are integral to industrial processes, enabling precise control over fluid flow in pipelines. They are used for throttling, isolation, and diversion of liquids and gases. Industries rely on these valves for their durability and ease of operation. Regular maintenance, such as valve adjustment, ensures optimal performance. Technical libraries often provide tutorials and guides for proper installation and troubleshooting. Manual valves remain essential for efficient and safe industrial operations across various sectors.
4.4 Oil and Gas Industry
Manual valves play a critical role in the oil and gas industry, ensuring safe and efficient operations in pipelines, refineries, and offshore platforms. They are used for controlling fluid flow, pressure regulation, and isolation of systems. Durable materials like steel and stainless steel are often used to withstand harsh environments. Regular maintenance, such as valve adjustment, is essential to prevent leaks and ensure compliance with safety standards. These valves are indispensable for maintaining operational integrity in the energy sector.
Advantages and Disadvantages
Manual valves offer simplicity, cost-effectiveness, and reliability, making them ideal for various applications. However, they require manual operation, which can be time-consuming and labor-intensive in large systems.
5.1 Benefits of Manual Valves
Manual valves are cost-effective, easy to install, and require minimal maintenance. They are highly reliable and suitable for various applications, including plumbing and HVAC systems. Their simplicity ensures long-term durability and resistance to wear. Additionally, manual valves do not rely on external power sources, making them ideal for systems where electricity is unavailable. Their straightforward design also reduces the risk of mechanical failure, ensuring consistent performance over time.
5.2 Limitations and Challenges
Manual valves have limitations, such as requiring physical effort to operate, which can be cumbersome in large systems. They are not suitable for remote operation, limiting automation capabilities. Additionally, manual valves may leak over time due to wear, leading to maintenance needs. Their lack of electronic control makes them less precise compared to automated alternatives, which can be a drawback in high-precision industrial environments. These challenges highlight their suitability for smaller, less complex applications.
Installation and Configuration
Manual valve installation involves connecting it to pipes, ensuring alignment, and securing it. Configuration varies by system, requiring precise setup for optimal flow control and functionality.
6.1 Step-by-Step Installation Guide
Install the manual valve by preparing tools and materials. Align the valve with the pipe system, ensuring proper connections. Secure it tightly using appropriate fittings. Test for leaks by turning the handle gently; Ensure the valve operates smoothly and is ready for system integration. Follow manufacturer instructions for specific configurations and safety precautions to avoid installation errors. Proper installation ensures optimal performance and longevity of the valve in various applications.
6.2 Configuration for Different Systems
Configuring manual valves varies by system type. For plumbing, ensure proper sizing and flow direction. In HVAC, set valves to regulate fluid or air accurately. Industrial systems may require specific actuation methods or additional controls. Always match valve type to system requirements, such as pressure and temperature ratings. Adjust settings according to manufacturer guidelines and test functionality before full operation. Proper configuration ensures efficient performance and compatibility with the system’s demands.
Maintenance and Repair
Regular maintenance ensures optimal valve performance. Inspect for wear, clean components, and replace worn parts promptly. Address leaks and corrosion early to prevent major repairs.
7.1 Regular Maintenance Tips
Regular maintenance is crucial for manual valves to ensure long-term functionality. Inspect for wear and tear, clean dirt, and grease moving parts. Check for leaks around seals and replace worn components promptly. Lubricate stems and threads to prevent corrosion. Schedule periodic disassembly to clean internal parts and ensure proper alignment. Regular maintenance prevents unexpected failures and extends valve lifespan, optimizing system performance. Always follow manufacturer guidelines for specific maintenance routines.
7.2 Common Repairs and Solutions
Common manual valve repairs involve replacing worn-out seats, seals, or O-rings to eliminate leaks. Damaged valve stems can be repaired or replaced to restore smooth operation. Corroded parts should be cleaned or substituted to prevent further damage. In cases of stuck valves, applying penetrating oil and gently tapping can free the valve. Always ensure the system is depressurized before starting any repair to avoid accidents. Regular maintenance helps reduce the need for frequent repairs.
Safety Considerations
Handling manual valves requires caution to prevent injuries and system damage. Always depressurize systems before maintenance and follow safety guidelines to ensure safe operation and avoid hazards.
8.1 Handling and Safety Precautions
When handling manual valves, wear protective gear like gloves and safety glasses to prevent injuries. Always turn off the system and depressurize it before maintenance. Ensure the valve is securely positioned to avoid accidental movement. Follow manufacturer guidelines and safety protocols to minimize risks. Regular inspections can help identify potential hazards early, ensuring safe and reliable operation. Proper training is essential for handling manual valves effectively.
8.2 Emergency Procedures
In case of a manual valve emergency, immediately isolate the system and shut off power. Evacuate the area if there’s a risk of leakage or exposure. Contact trained professionals to handle repairs. Keep emergency contact information accessible. Regular drills ensure preparedness. Always follow established protocols to minimize risks and ensure safe resolution. Prompt action can prevent escalation and protect both personnel and equipment.
Manual valves are essential for controlling fluid flow, offering simplicity and reliability. Their versatility across industries ensures continued relevance in modern systems.
9.1 Summary of Key Points
Manual valves are critical components in fluid control systems, offering simplicity and reliability. They come in various types like gate, globe, and ball valves, each suited for specific applications. These valves are widely used in plumbing, HVAC, and industrial processes. Their operation relies on mechanical or actuated controls, ensuring efficient flow regulation. Regular maintenance and proper installation are essential for optimal performance and longevity.
9.2 Final Thoughts and Recommendations
Manual valves remain indispensable in modern systems due to their durability and simplicity. For optimal performance, regular maintenance and adherence to installation guidelines are crucial. Users should consider valve type and material based on application requirements to ensure reliability. Following safety precautions and manufacturer instructions is essential for safe operation. Proper selection and care can extend valve lifespan and maintain system efficiency.
Leave a Reply
You must be logged in to post a comment.